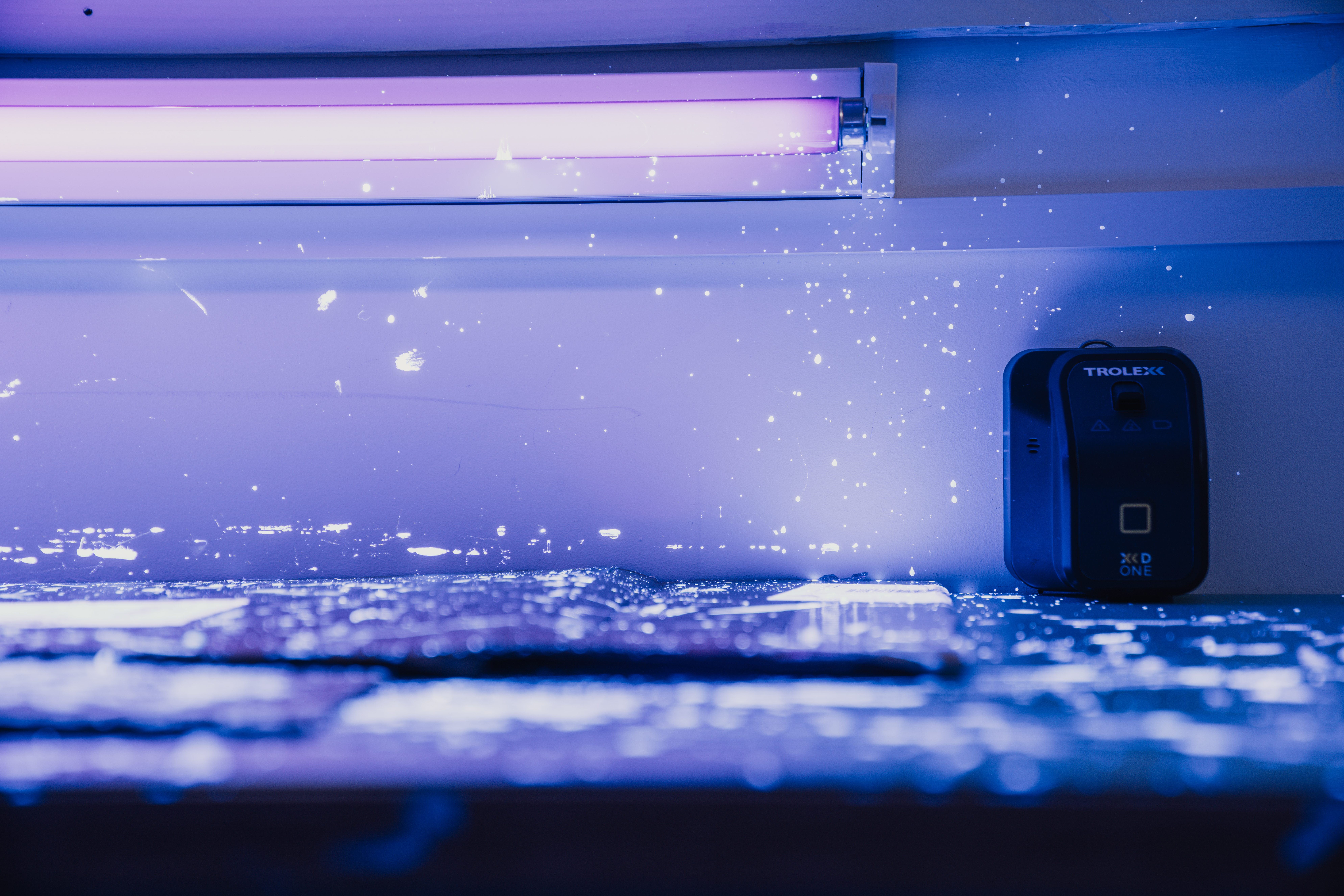
See why the world’s biggest mining and industrial corporations put Trolex equipment at the heart of their multi-billion dollar projects, when productivity, reputation and the health of their workforce depend on it.
Featured
Latest
Filter by:
See why the world’s biggest mining and industrial corporations put Trolex equipment at the heart of their multi-billion dollar projects, when productivity, reputation and the health of their workforce depend on it.
Filter by: